Vector control, also known as field-oriented control (FOC), is an advanced method of controlling AC motors, particularly three-phase induction and synchronous motors. It allows for precise control of both the magnitude and direction of the motor's magnetic field, enabling improved performance in terms of torque, speed, and overall dynamic response.
Key Concepts of Vector Control
- Separation of Torque and Flux Components:
- In an AC motor, the stator current can be decomposed into two orthogonal components: one that produces torque (the torque-producing component) and one that produces the magnetic flux (the flux-producing component).
- Vector control separates these components and controls them independently, similar to how DC motors are controlled. This decoupling allows for more precise and efficient control of the motor.
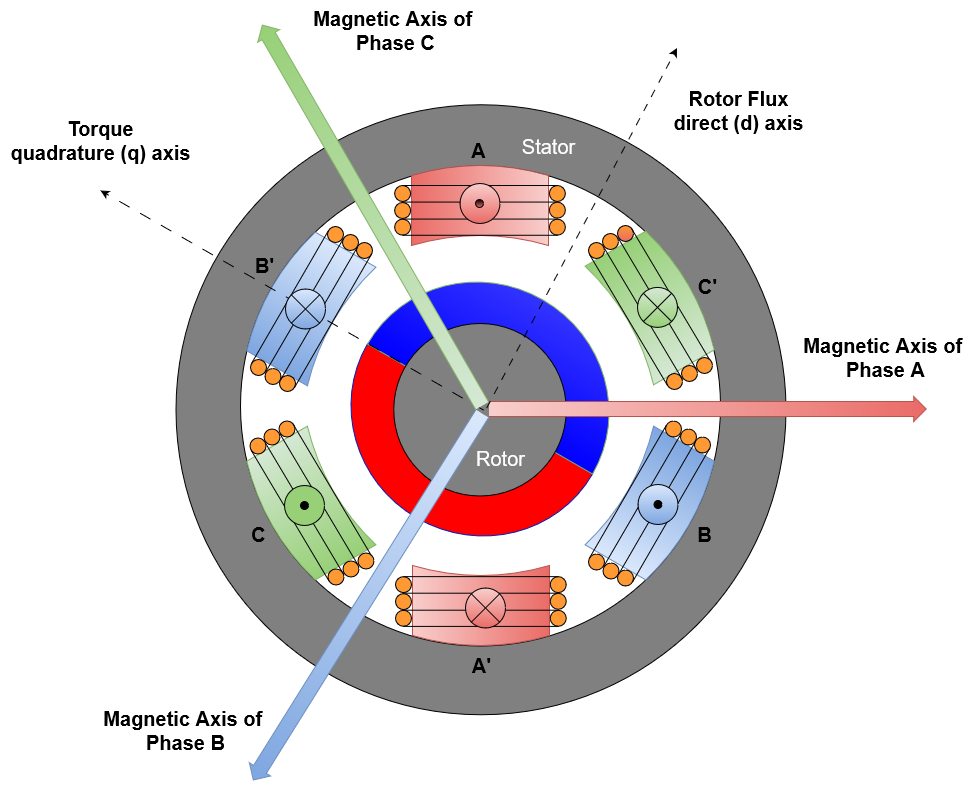
Coordinate Transformation:
- The motor's three-phase currents are transformed into a two-axis coordinate system (typically called the d-q axis) using mathematical transformations like the Clarke and Park transformations.
- In this transformed coordinate system, the d-axis is aligned with the rotor flux, and the q-axis is orthogonal to it. This transformation simplifies the control of the motor's magnetic field and torque.
Control Loops:
- Separate control loops are used to regulate the d-axis (flux) and q-axis (torque) components. This allows for independent control of motor torque and flux, enabling the motor to respond quickly and efficiently to changes in load or speed commands.
Pulse Width Modulation (PWM):
- The control signals generated by the vector control algorithm are fed into a PWM inverter, which converts the control signals into the appropriate three-phase voltages that drive the motor.
Benefits of Vector Control
Precise Torque Control: By independently controlling the torque and flux components, vector control allows for precise torque generation, even at low speeds.
Fast Dynamic Response: The decoupling of torque and flux allows the motor to quickly respond to changes in load or speed, making it suitable for applications requiring rapid acceleration and deceleration.
Efficient Operation: Vector control optimizes the motor's performance, leading to higher efficiency, especially under varying load conditions.
Smooth Operation: It provides smoother operation with less torque ripple compared to traditional control methods, making it ideal for applications requiring high-quality motion control.
Applications
Vector control is commonly used in applications where high performance is required, such as:
- Electric vehicles
- Industrial drives and automation
- Robotics
- CNC machines
- Servo systems
In summary, vector control enhances the performance of AC motors by enabling independent control of torque and magnetic flux, resulting in better efficiency, precision, and dynamic response.
Answer from OpenAI